W handlu detalicznym zaprzestaje się stosowania plastikowych toreb, ruchy ekologiczne nabierają rozpędu, ponieważ klimat, zwierzęta i ochrona środowiska stają się coraz ważniejsze. Transformacja społeczna, odpowiedzialność za zrównoważony rozwój oraz zmiany w sposobie wykorzystania tworzyw sztucznych nie pozostają niezauważone przez przemysł. Wiele firm dba o to, by gospodarka o obiegu zamkniętym zajmowała priorytetowe miejsce. Przykład igusa, który jest specjalistą od tworzyw sztucznych, pokazuje, w jaki sposób firmy mogą wykorzystywać innowacje ekologiczne, aby nadać impet rosnącemu znaczeniu m.in. takich kwestii, jak recykling plastiku.
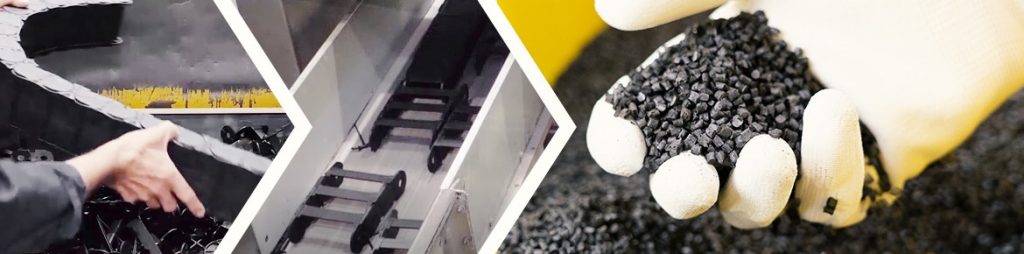
W naszym głównym zakładzie w Kolonii, opracowujemy i testujemy zoptymalizowane trybologicznie, wysokowydajne tworzywa sztuczne do zastosowań ruchomych. Są to, jak już zapewne wiecie, łożyska ślizgowe, łożyska kulkowe, łożyska samonastawne, e-prowadniki, przewody, materiały do druku 3D i ekonomiczna robotyka, oparta na tworzywach sztucznych.
Zalety wysokowydajnych polimerów są oczywiste: nie wymagają one żadnego dodatkowego smarowania, ponieważ dodajemy do polimerów bazowych między innymi stałe środki smarne.
W samych Niemczech co roku sprzedaje się ponad milion ton oleju smarowego, z czego połowa trafia do środowiska. W przypadku technologii łożysk ślizgowych iglidur, zanieczyszczenie środowiska możemy zredukować dzięki brakowi zewnętrznych środków smarnych. Przyczynia się to również do tego, że tworzywa ruchome są odporne na kurz i brud. Dzięki czemu brud nie może przywierać do łożyska, więc nie blokuje ich i nie powoduje awarii.
Mniej mikroplastiku, dzięki tworzywom sztucznym odpornym na ścieranie
Zarówno w rzeczywistej eksploatacji, jak i podczas 15000 testów tribologicznych, przeprowadzanych co roku w laboratorium badawczym o powierzchni 3800 m2, nasze motion plastics udowadniają, jak bardzo są odporne na kurz i zużycie.
Mniejsze ścieranie oznacza mniejsze zanieczyszczenie środowiska mikroplastikami, a także znacznie dłuższą żywotność komponentów. Nie ma również konieczności tak szybkiej wymiany maszyny lub poszczególnych części.
Co więcej, jeśli te komponenty są również “inteligentne” i dokładnie przewidują swoją żywotność podczas rzeczywistej eksploatacji, regularna konserwacja i wymiana nie są już konieczne. e-prowadnik, kabel lub łożysko ślizgowe są bowiem wymieniane dokładnie wtedy, gdy jest to konieczne.
Takie rozwiązanie może również wydłużyć żywotność poszczególnych komponentów w aplikacji. Nie ma potrzeby rutynowej wymiany części, która nadal działa prawidłowo.
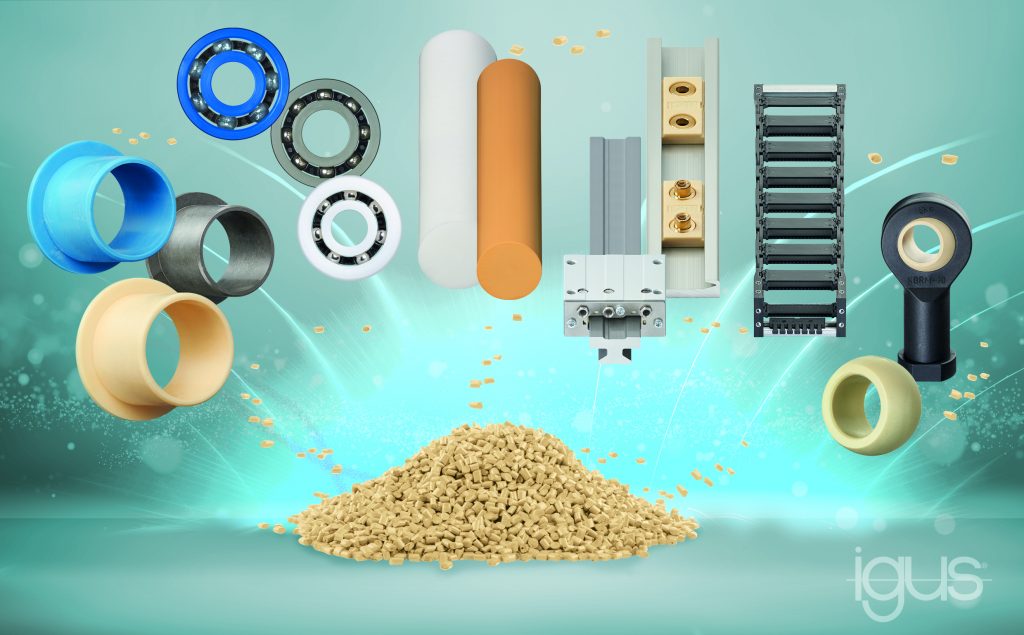
Gospodarka o obiegu zamkniętym, czyli produkcja efektywnie wykorzystująca zasoby
Zastosowanie tworzywa sztucznego ma kolejną zaletę: przy produkcji wykorzystujemy tylko ułamek energii, która byłaby potrzebna do wykonania metalowej wersji elementu. Podczas gdy produkcja jednej tony aluminium pochłania 600 MJ energii, a tona stali zużywa 320 MJ, tworzywa sztuczne wymagają jedynie 160 MJ.
Energię oszczędzają również maszyny, które opierają się na polimerach igus. Niska waga elementów maszyny oznacza, że do ruchu potrzeba mniej energii. Na przykład, w przypadku e-prowadników serii P4.1, do poruszania systemu e-prowadników potrzeba 57% mniej energii napędowej.
Łatwy recykling plastiku…
Przychodzi jednak taki dzień, w którym nawet najtrwalsze i najdłużej działające części z tworzywa sztucznego muszą zostać zezłomowana. Wtedy też pojawia się kwestia możliwości recyklingu. I to właśnie tutaj realizujemy swoje inicjatywy w zakresie recyklingu. Dzięki polimerowi iglidur N54 opracowaliśmy pierwsze standardowe łożysko ślizgowe, które składa się głównie z biopolimerów.
Jednocześnie poddajemy w igus recyklingowi 99% odpadów z tworzyw sztucznych w swojej fabryce i ponownie wprowadzamy je w niewielkich ilościach do procesu produkcyjnego. Warto tutaj zaznaczyć, podając za „Plastic Atlas” z 2019, że tylko 16% odpadów z tworzyw sztucznych, produkowanych w Niemczech, jest ponownie wykorzystywanych do wytwarzania nowych produktów.
Nawet jeśli trwałe produkty z tworzyw sztucznych, takie jak e-prowadniki, nie są porównywalne z produktami codziennego użytku, które można wyrzucić, po zakończeniu okresu użytkowania, nadal pojawia się kwestia ich utylizacji. Zwykle prowadnik jest usuwany razem z innymi odpadami z tworzyw sztucznych. Recykling plastiku wykorzystywanego do produkcji prowadników rzadko ma miejsce. Dzieje się tak dlatego, że koszt oddzielenia różnych materiałów w produkcie i przetworzenia ich, w celu uzyskania nadającego się do użytku granulatu, jest zbyt wysoki. Dlatego, w większości fabryk, zwykłą procedurą jest usuwanie e-prowadników z maszyn i wrzucanie ich do pojemników na odpady przemysłowe. W większości przypadków tworzywa sztuczne są następnie spalane.
… czyli program recyklingu „eko-prowadnik” firmy igus
Firma igus oferuje obecnie przyjazną dla środowiska alternatywę, czyli program recyklingu „eko-prowadnik”. Celem programu jest specjalny recykling plastiku z prowadników kablowych i ponowne wykorzystanie go w nowych produktach. W tym celu, użytkownicy mogą wysyłać swoje stare, nieużywane plastikowe e-prowadniki do nas (po ich uprzednim oczyszczeniu), niezależnie od tego, kto był producentem prowadnika. Sortujemy, czyścimy, rozdrabniamy i pakujemy otrzymane tworzywa sztuczne. Następnie możemy je wykorzystać w igusie lub udostępniamy innym firmom, do produkcji wysokiej jakości produktów technicznych. Za oddanie prowadnika kablowego do recyklingu, klient otrzymuje od nas bon towarowy, na zakupy w igusie.
“Firma igus bierze na siebie tę odpowiedzialność i dzięki swojemu programowi recyklingu „eko-prowadnik” przyczynia się do zmniejszenia ilości odpadów z tworzyw sztucznych i usprawnienia procesu recyklingu” – mówi Frank Blase, prezes firmy igus GmbH.
Tylko w 2020 roku, kilka ton e-prowadników zostało poddanych recyklingowi. Odzyskany z nich plastik, został ponownie wprowadzony do procesu produkcyjnego.
Powrót do oleju mineralnego za pomocą wody, wysokiej temperatury i ciśnienia
Na początku 2020 roku wykonaliśmy w igus kolejny ważny krok w dziedzinie recyklingu. “Przed rokiem artykuł w Frankfurter Allgemeine Zeitung (niemiecka gazeta) zwrócił moją uwagę na technologię katalitycznych reaktorów hydrotermalnych. Następnie skontaktowałem się z niemieckim wynalazcą, profesorem Thomasem Maschmeyerem, w Sydney” – relacjonuje Frank Blase. Siedem miesięcy później, po intensywnych badaniach, igus zainwestował cztery miliony funtów brytyjskich (4,7 mln euro) w Mura Technology Limited. Tym samym zainwestował również w budowę pierwszej instalacji Cat-HTR™. Na początku 2021 roku zwiększyliśmy swoją inwestycję do łącznej kwoty 5 mln euro.
Opatentowana technologia katalitycznego reaktora hydrotermalnego została opracowana w 2007 roku. Przez dziesięć lat była testowana w zakładzie pilotażowym w Australii. Dzięki technologii Cat-HTR™ odpady z tworzyw sztucznych, których recykling był wcześniej niemożliwy, można w ciągu 20 minut przekształcić z powrotem w olej. Jest to procedura znacznie bardziej efektywna pod względem wykorzystania zasobów niż wydobywanie paliw kopalnych z ziemi. Do oddzielenia cząstek i ponownego ich połączenia wykorzystuje się jedynie wodę, wysoką temperaturę i ciśnienie. Tylko jeden zakład może przetworzyć 20 000 ton plastiku rocznie i zredukować emisję CO2 o 28 180 ton. Odpowiada to rocznemu zużyciu 5983 samochodów lub rocznemu zapotrzebowaniu na energię 4914 gospodarstw domowych.
Tradycyjny recykling tworzyw sztucznych a recykling z Cat-HTR™
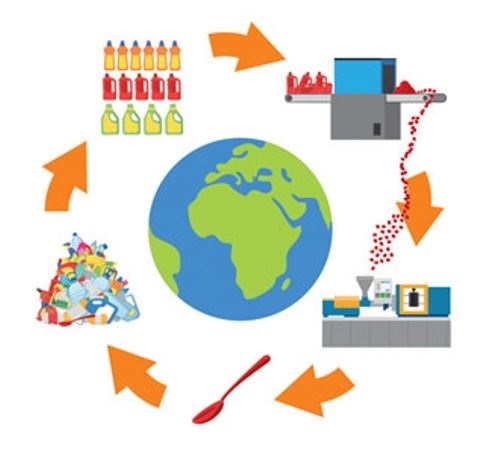
W przypadku tradycyjnego recyklingu tworzyw sztucznych – stosowanego również przez igus w naszym programie recyklingu „eko-prowadnik” – wszystkie odpady przed rozdrobnieniem muszą być posortowane według składników. Granulki można następnie wykorzystać do produkcji nowych produktów polimerowych metodą formowania wtryskowego lub wytłaczania.
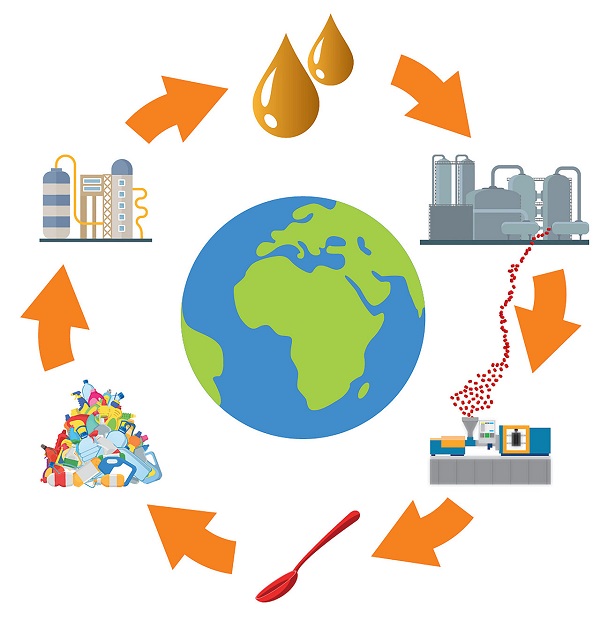
Technologia Cat-HTR przekształca niesortowane odpady z tworzyw sztucznych w olej w ciągu 20 minut, oszczędzając zasoby naturalne. Powstałą w ten sposób ropę naftową, możemy wykorzystać jako smar, wosk lub do produkcji nowych, wysokiej jakości plastikowych granulek.
Recykling plastiku przy użyciu technologii Cat-HTR™
Pierwsza komercyjna instalacja Cat-HTR ™, w zakładzie przemysłowym Wilton International w Wielkiej Brytanii, jest obecnie na etapie planowania. W marcu rozpoczyna się tam budowa pierwszego zakładu CAT-HTR ™ firmy Mura. Ma on rozpocząć działalność w drugiej połowie 2022 roku.
Firmy zajmujące się odpadami dostarczają je, aby osiągnąć swoje cele w zakresie recyklingu. Z odpadów uzyskuje się następnie ropę, którą można kupić po cenie podobnej do tej, jakiej żąda się za ropę kopalną. W Wilton mają powstać cztery katalityczne reaktory hydrotermalne, które będą przetwarzać rocznie ponad 80 000 ton odpadów z tworzyw sztucznych. Obecnie Mura Technology pozyskała KBR jako wyłącznego partnera licencjonowanego do dalszej ekspansji. KBR zatrudnia 28 000 pracowników i działa w ponad 80 krajach. Funkcjonuje między innymi jako projektant, wykonawca prac inżynieryjnych oraz operator rafinerii i fabryk chemicznych. “Jesteśmy zaangażowani w osiągnięcie stanu równowagi w świecie tworzyw sztucznych za pomocą rozwiązań technicznych” – mówi Frank Blase.