Kiedy aplikacje i mechanizmy niezbędne do prawidłowego działania naszej firmy zawodzą, zaczynają się problemy. Przestój w pracy na produkcji generuje niepotrzebne koszty, dodatkowe zmiany czy niezadowolenie, a nawet utratę klientów. Podpowiadamy, jak radzić sobie w takich sytuacjach i skrócić długie przestoje w procesie produkcyjnym?
Co to jest przestój?
Przestój to okres, w którym sprzęt produkcyjny jest w trybie offline lub nie jest dostępny dla procesu produkcyjnego, ponieważ wymaga konserwacji lub jest uszkodzony. Może to powodować zarówno znaczne koszty, jak i inne niepożądane skutki.
Jakie mogą być skutki przestojów?
- Opóźnienie w bieżącej produkcji
- Opóźnienie w kolejnych procesach
- Niewykorzystani pracownicy lub dodatkowe zmiany
- Niezadowoleni klienci, a nawet utrata klientów
- Osłabienie konkurencyjności
- Możliwe kary umowne za niewykonanie zlecenia
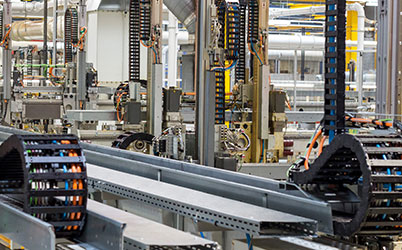
Rodzaje przestojów
Rozróżnia się dwa rodzaje przestojów – zaplanowane i niezaplanowane.
Przestój zaplanowany obejmuje planowe czynności konserwacyjne, które należy przeprowadzić w określonym czasie. Firma może naprawić problem związany z maszyną, zanim stanie się on zbyt duży. Nie można jednak całkowicie wykluczyć ryzyka niepowodzenia.
W przypadku nieplanowanego przestoju, urządzenie jest używane do momentu wystąpienia usterki. Awaria maszyny może prowadzić do długich przerw w łańcuchu produkcyjnym.
3 sposoby na skrócenie przestojów
- Ocena ryzyka
Ocena ryzyka jest najszybszym i najskuteczniejszym sposobem ograniczenia przestojów i związanych z tym wysokich kosztów finansowych w przyszłości.
W szczególności zużywanie się maszyn stanowi znaczne ryzyko dla produkcji. Pomimo postępów w dziedzinie systemów sterowania, wielu producentów nadal pracuje z urządzeniami, które mają od 15 do 20 lat. Komponenty często nie są już dostępne lub są wytwarzane za granicą, co prowadzi do długich czasów dostawy.
Dostępność maszyn i znajomość sieci produkcyjnej tworzy różnicę między przestojami trwającymi kilka godzin, a przestojami trwającymi kilka miesięcy. Sposobem oceny i identyfikacji ryzyka może być metoda FMEA, czyli Failure Mode and Effects Analysis.
- Szkolenie pracowników oraz regularna wymiana doświadczeń
Większość awarii maszyn wynika z błędu ludzkiego. Dlatego tak ważne jest kompleksowe przeszkolenie pracowników w zakresie obsługi maszyn.
Należy również nauczyć pracowników rozpoznawania i rozumienia faktycznych skutków przestojów spowodowanych niewłaściwym użytkowaniem maszyn i urządzeń.
W związku z tym, intensywna komunikacja między menadżerami a pracownikami, jest ważnym warunkiem poprawy wydajności i ograniczenia przestojów.
- Stosowanie czujników w celu wykrycia problemów na wczesnym etapie
Jeśli zastosujemy czujniki, oznaki nieuchronnych przestojów będziemy mogli często wykryć na długo przed faktyczną awarią. Czujniki mogą mierzyć poziom wibracji i hałasu, a także zużycie niektórych elementów maszyny.
Jeśli zintegrujemy je z jednostkami produkcyjnymi, możemy wykryć problemy i podjąć odpowiednie działania z wyprzedzeniem, zanim doprowadzą one do przestojów.
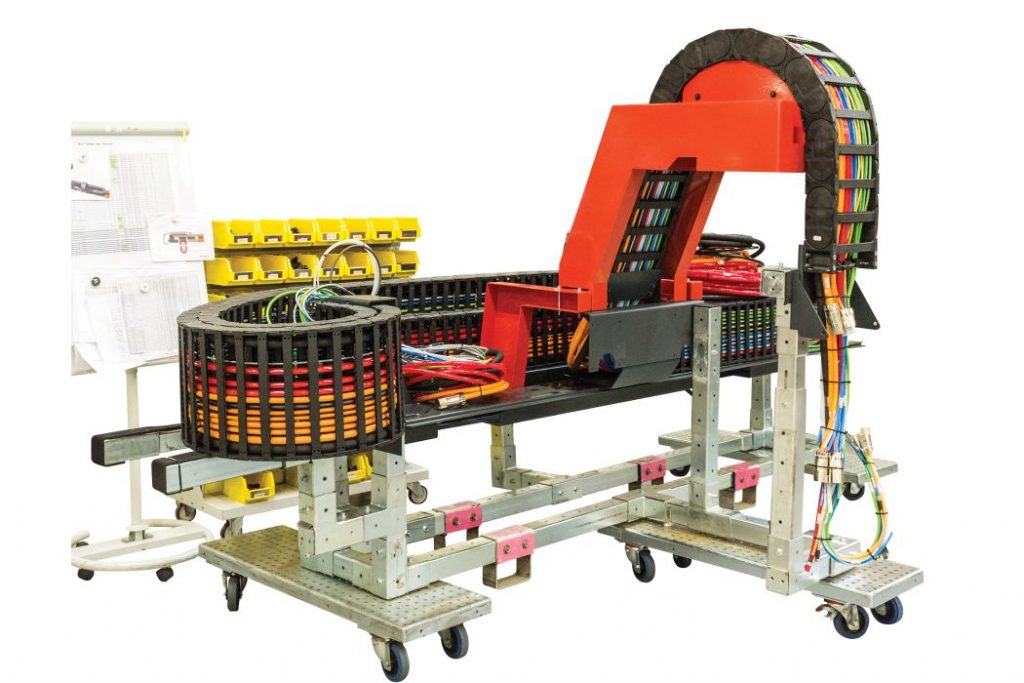
igus® pomaga w skróceniu przestojów
igus® pomaga skrócić przestoje dzięki możliwości zastosowania readychain®i readycable®.
Jeśli prowadniki kablowe zostaną do nas dostarczone z uprzednio zamontowanymi przewodami, a przewody z zamontowanymi złączami (readycable®), to otrzymujemy rozwiązanie plug-and-play. Oznacza to, znaczne skrócenie czasu wymiany, zarówno podczas zaplanowanych, jak i niezaplanowanych przestojów.
Co więcej, w przypadku wystąpienia niezaplanowanych przestojów, będziemy mogli zredukować przestrzeń magazynową. Związane jest to z tym, że gotowy do połączenia system pochodzi od jednego dostawcy i może zostać do nas dostarczony dokładnie w czasie wymiany.
Aktualnie w przemyśle rozwija się konserwacja predykcyjna, która związana jest z przemysłem 4.0. Przykładem mogą tu być łańcuchy energetyczne, które wyposażono w czujniki mające za zadanie wczesne wykrycie problemów.
W różnych wersjach można wykryć pęknięcie pojedynczego ogniwa łańcucha energetycznego, ocenić warunki otoczenia pracy, na przykład temperaturę, zużycie w otworze sworznia ogniwa łańcucha lub zużycie na zewnątrz ogniwa prowadnika, w przypadku zastosowań ślizgowych.
Różne systemy monitorowania można skonfigurować offline i online, a stan urządzenia można sprawdzić w dowolnym momencie.
Takie systemy czujników nie tylko pomagają reagować na awarie maszyn na wczesnym etapie. Pozwalają również wydłużyć ich żywotność.